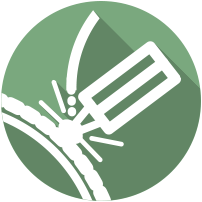
Laser Cladding
Laser cladding can be applied to high-volume surfacing, complex geometries, irregularly-shaped parts, multidimensional profiles, and threaded areas.
The damaged surface area of the component is machined to precise specifications in preparation for the Laser Cladding process.
Laser Cladding Advantages
- Selective hardness ranges
- Various levels of corrosion resistance
- Matching substrate chemistry
- Minimal inter-metallic dilution
- Low heat input
- Low thermal distortion
- Narrow heat-affected zone
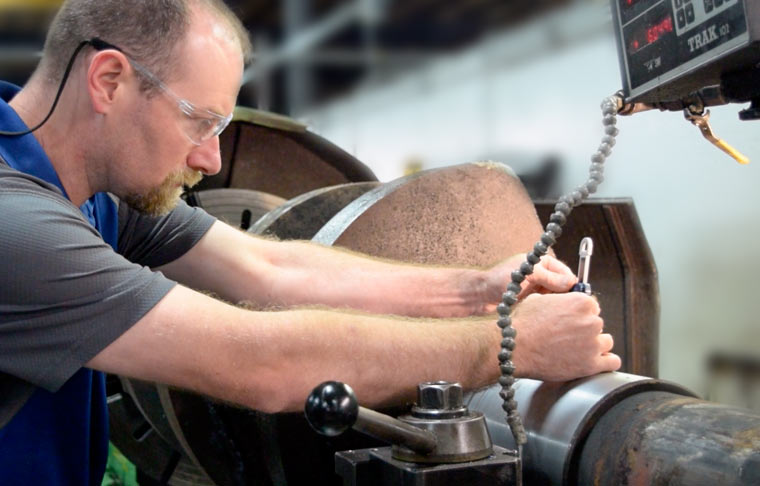
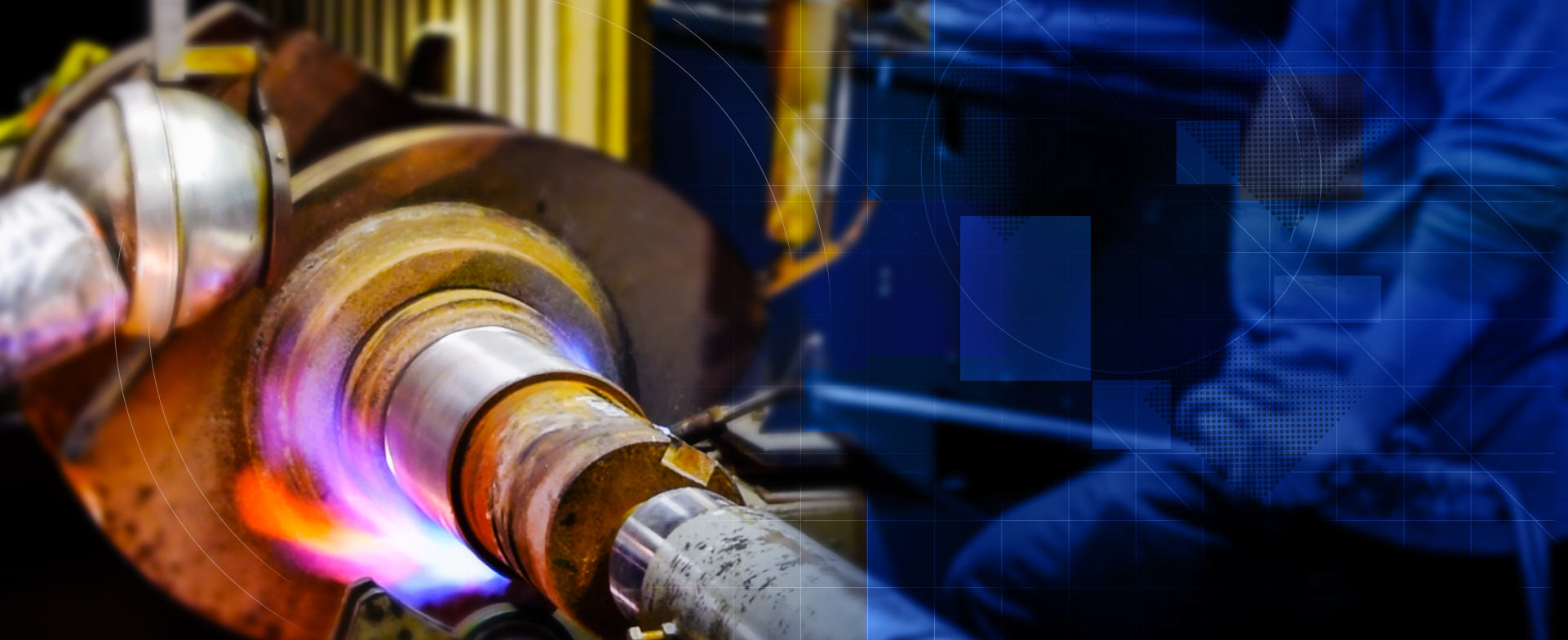
The machined component is sent to one of Swanson’s laser cladding facilities.
With the cladding process complete, the component is machined to OEM specifications, finished and inspected.
Swanson maintains four high-powered fully automated laser cladding systems with size capabilities of less than 1″ in diameter to 48″ in diameter and up to 80 feet in length.
This high density, low thermal input process can apply a multitude of surface coatings at specified chemistry with minimal heat effect and dimensional distortion.
Swanson’s component specifications for Laser Cladding:
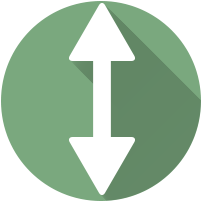
80 feet long
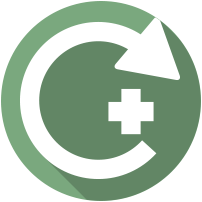
48 inches in diameter
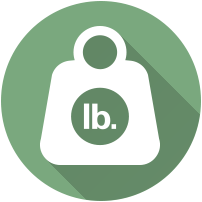
40,000 pounds
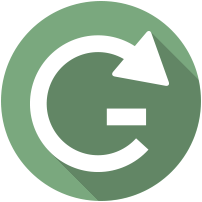
1 inch min. diameter
•Exact dimensions available upon consultation
Swanson’s highly capable laser cladding stations can perform Outside and Inside Diameter Restoration, Gear and Irregular Shape Restorations.
Laser Cladding can also be utilized to resurface worn or damaged cylinders, rolls and pistons to prime working condition.
Highly-Engineered to OEM Standards for Rigorous Applications in the Mobile, Industrial, Marine and Offshore Markets
ALLOY | APPLICATION | TYPE | TYPICAL HARDNESS |
Austenitic Stainless Steels | Corrosion resistance and welding | 309L | 316L | 347 | 20-22 HRC |
Cobalt Based | Corrosion and high-temperature wear resistance | Alloy 6 ULTIMET® |
45-50 HRC 28-33 HRC |
Precipitation-Hardening Stainless Steel | Corrosion and wear resistance | 17-4 P-H | 33-38 HRC |
Martensitic Stainless Steels | Wear resistance | 410L/410 420 431 |
38-42 / 44-46 HRC 50-55 HRC 50-53 HRC |
Nickel-Based Alloys | Corrosion resistance | Inconel 625 Inconel 718 C-22 | C-276 |
22-25 HRC 22-25 HRC < 24 HRC |
Tungsten Carbide | Abrasive wear resistance | 60% WC in Nickel binder | 74-76 HRC |
Advantages | Laser Clad | HVOF | PTA |
Metallurgical Bond | Yes | No (mechanical) | Yes |
Low Dilution | < 5% | — | < 10% |
Heat-Affected Zone HAZ | 0.020”- 0.040” typical | — | 0.080” – 0.100” |
Minimal Distortion | Yes | Yes | More than laser |
Laser | Max Diameter | Max Length | Max Weight |
14 kW CO2 | 40 inches | 58 feet | 40,000 lbs |
12 kW YAG | 48 inches | 80 feet | 40,000 lbs |
8 kW CO2 | 36 inches | 120 inches | 2,000 lbs |
12 kW YAG | 25 inches | 72 inches | 1,200 lbs |